Schneider Electric Lexium 62 ILM Integrated Servo Motor
ILM0701P22A0000: A Technical Deep Dive
The Schneider Electric Lexium 62 ILM series introduces the ILM0701P22A0000, a variant engineered for applications demanding multiturn absolute positioning, high-speed precision, and rugged
environmental resistance—all without an integrated brake. This model integrates a 1.1 Nm
brushless motor, a 6,000 rpm speed capability, a 23-bit multiturn absolute encoder, and an IP65-rated housing into a compact 1.2 kg unit. Its 14mm round shaft with keyway and battery-free multiturn tracking make it ideal for rotary
indexing tables, wind turbine yaw systems, and outdoor automation.
Below is a detailed technical review, emphasizing its unique
design, performance, and applications.
Technical Specifications Table
Parameter | ILM0701P22A0000 Specification |
---|
Model Code | ILM0701P22A0000 |
Motor Type | Integrated Servo Motor (Motor + Drive + Encoder) |
Nominal Torque | 1.1 Nm (continuous) |
Peak Torque | 3.3 Nm (1-second burst) |
Rated Speed | 6,000 rpm |
Power Output | 400W (at 6,000 rpm) |
Encoder Resolution | 23-bit multiturn absolute (8,388,608 positions/rev, 16-bit multiturn) |
Brake | Not included (external brake optional) |
Shaft Configuration | 14mm round shaft with keyway (versatile coupling options) |
Communication Protocols | EtherCAT, CANopen, Modbus TCP/IP (via Lexium 62 drive) |
Protection Class | IP65 (motor and connector side) |
Ambient Temperature Range | Operating: -10°C to +50°C / Storage: -20°C to +70°C |
Voltage Supply | 48V DC (24–55V DC range) |
Current Draw | 8.5A (peak), 4.2A (RMS) |
Weight | 1.2 kg |
Mounting Interface | IEC B14 flange |
Vibration Resistance | 5G (10–200 Hz, IEC 60068-2-6) |
Shock Resistance | 50G (IEC 60068-2-27) |
Certifications | CE, UL, cUL, RoHS, REACH, IP65 |
Product Availability | Non-Stock (Special Order, 4–6 Weeks Lead Time) |
1. Design Innovation: IP65 Protection and Multiturn Encoder
The ILM0701P22A0000 combines two critical features for harsh
environments:
IP65-Rated Housing:
- Dust Tight and Water Resistant: Withstands low-pressure water jets, making it suitable for
washdown applications in food processing or outdoor use.
- Sealed Connectors: M12 connectors with O-ring seals prevent moisture ingress.
Multiturn Absolute Encoder:
- 23-bit Resolution: Combines 8 million single-turn positions with 16-bit multiturn tracking (65,536 revolutions), enabling precise position tracking across
extended rotations.
- Battery-Free Operation: Utilizes energy harvesting from motor rotation to maintain
multiturn data during power cycles.
2. Performance Benchmarks
Torque and Speed:
- The 1.1 Nm continuous torque suits steady-state operations, while the 3.3 Nm peak torque enables rapid acceleration in applications like packaging
machinery.
- At 6,000 rpm, it excels in high-speed tasks such as spindle drives or
centrifugal separators.
Encoder Accuracy:
- Multiturn Resolution: Enables applications like rotary tables or wind turbine yaw
systems, where tracking multiple revolutions is critical.
- Latency: <1 μs feedback update rate ensures real-time control in
synchronized motion systems.
3. Applications
The ILM0701P22A0000 is tailored for:
- Rotary Indexing Tables: CNC machines, assembly lines, and food packaging systems
requiring precise angular positioning.
- Wind Turbine Yaw Systems: Multiturn tracking ensures accurate blade orientation relative to
wind direction.
- Outdoor Equipment: Solar trackers, construction machinery, and agricultural robots.
- Medical Imaging: CT scanners and radiation therapy systems needing sub-degree
precision over thousands of rotations.
- Automotive Testing: Dynamometers and engine test stands requiring repeatable
positioning.
4. Technical Advantages
Environmental Robustness:
- Wide Temperature Range: Operates from -10°C to +50°C, suitable for freezers or heated
industrial settings.
- Corrosion Resistance: Coated housing resists chemical exposure in food processing.
Connectivity:
- EtherCAT FSoE: Enables safety communication over EtherCAT for integrated safety
architectures.
- Dual-Port EtherCAT: Supports line topology for daisy-chained motion axes.
Energy Efficiency:
- Up to 95% efficiency reduces energy consumption, while regenerative braking function
(when paired with an external brake) recovers kinetic energy.
5. Installation and Commissioning
Mounting:
- IEC B14 flange with a 14mm round shaft (with keyway) ensures secure
coupling to mechanical loads.
- Adjustable mounting feet accommodate misalignment during
installation.
Wiring:
- A single 48V DC supply powers the motor.
- Dedicated encoder feedback terminals (M12 connector) simplify
integration with controllers.
Software Tools:
- Schneider Electric’s SoMove software streamlines parameter tuning, diagnostics, and firmware
updates.
- Preloaded motion profiles (e.g., S-curve, trapezoidal) reduce
programming effort.
6. Maintenance and Troubleshooting
Preventive Maintenance:
- The encoder’s self-diagnostics flag deviations in position
accuracy.
- Regular inspection of cooling fins (if forced air is used) prevents
thermal overload.
Error Handling:
- LED indicators on the motor housing provide real-time status
feedback (e.g., overcurrent, overvoltage).
- Fault codes are logged internally for post-mortem analysis via
SoMove.
7. Compatibility and Accessories
Optional Add-Ons:
- External Brake Kit: For applications requiring holding torque (e.g., vertical axes).
- Gearboxes: Planetary or helical options to increase torque density.
- Cables: Pre-terminated motor cables (1m, 2m, 5m lengths) with M12/M23
connectors.
- IP69K Connectors: For high-pressure washdown environments in food processing.
Controller Compatibility:
- Works seamlessly with Schneider Electric’s PacDrive 3 and Modicon M580 PLCs.
- Third-party controller support via open-source EtherCAT stacks.
8. Environmental and Safety Compliance
- RoHS/REACH Compliance: Ensures absence of hazardous substances.
- Low Noise Emission: Operates at <70 dB(A), suitable for noise-sensitive
environments.
- Safety Functions: Supports STO (Safe Torque Off) and SS1 (Safe Stop 1) per ISO
13849-1.
9. Ordering and Availability
As a Non-Stock item, the ILM0701P22A0000 requires a 4–6 week lead time from Schneider
Electric’s manufacturing facilities. Customers are advised to:
- Confirm regional availability through Schneider Electric’s eCommerce portal or authorized distributors.
- Specify optional accessories (gearboxes, cables) during order
placement to avoid delays.
10. Frequently Asked Questions (FAQs)
Q1: What is the difference between single-turn and multiturn
encoders?
A1: Single-turn encoders track positions within one revolution,
while multiturn encoders track thousands of revolutions, critical
for rotary tables or wind turbines.
Q2: Can this motor operate in a food-grade application?
A1: Yes, with an optional stainless steel shaft and IP69K-rated
connectors for high-pressure washdown.
Q3: Is the multiturn encoder resolution upgradeable?
A3: No, the 23-bit resolution is fixed. For higher precision,
consider the ILM1202 model (24-bit).
Q4: Can I use this motor for vertical applications without a brake?
A4: Yes, but an external brake is recommended to prevent
backdriving in case of power failure.
Conclusion
The Schneider Electric Lexium 62 ILM0701P22A0000 integrated servo
motor redefines precision and durability in harsh environments. Its
combination of an IP65-rated housing, multiturn absolute encoder,
and 1.1 Nm torque makes it indispensable for applications like
outdoor machinery or food processing. While its Non-Stock status
reflects its specialized nature, the 4–6 week lead time is
justified by the motor’s advanced capabilities and Schneider
Electric’s rigorous quality control. For engineers seeking a
compact, high-performance servo solution with environmental
robustness and multiturn tracking, the ILM0701P22A0000 sets a new
benchmark in its class.
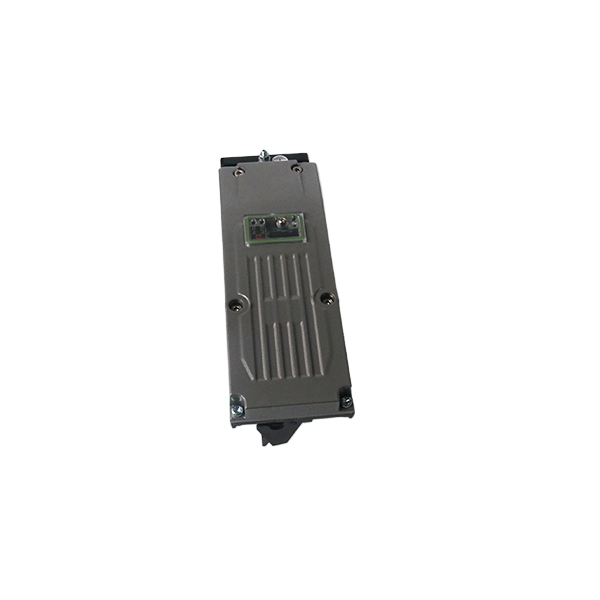